A submersible pump’s mechanical seal is the most critical component in keeping the pump in operation. The seal has a challenging job-keep a submerged electrical motor protected from the outside elements. Take a closer look at one of the R-Series pump mechanical seal configurations and the steps RIG has taken to keep your pump running longer in the most demanding applications.
The Internal Double Slurry Seal is a double or (back to back) mechanical seal in which a single spring engages a set of seal faces at both ends. The two models used are the Type 21 from John Crane and ED560 from Eagle Burgmann.
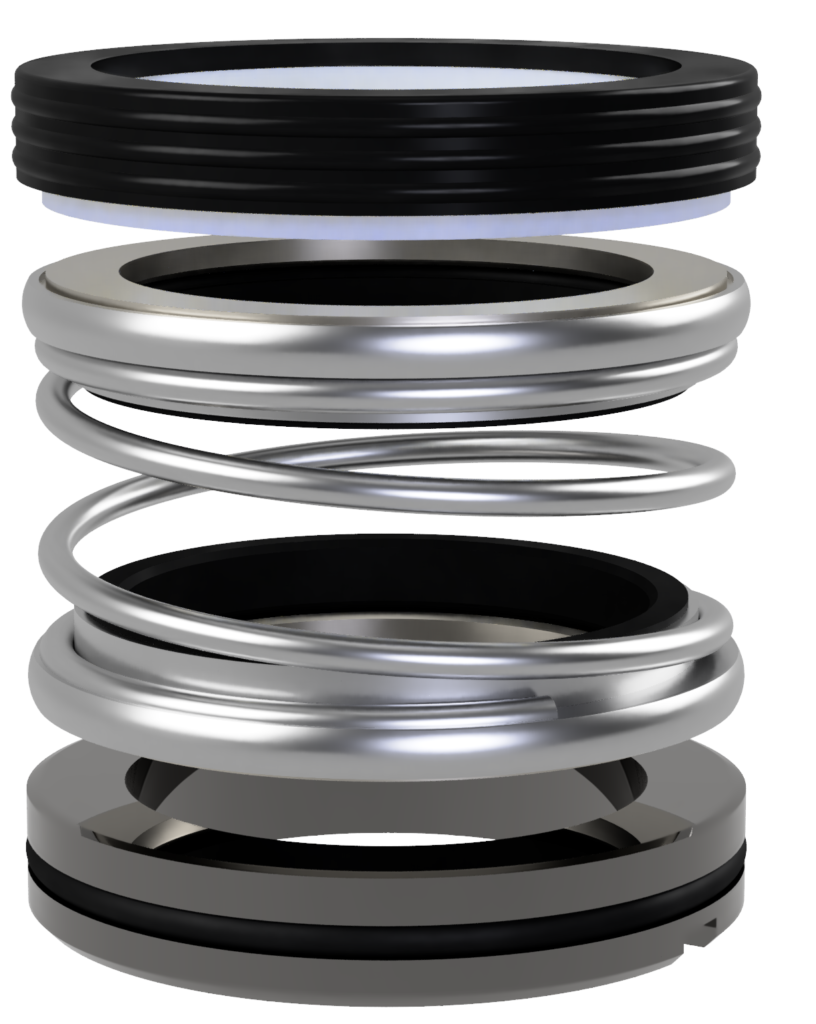
The seal is installed in the motor oil chamber and operates away from the process fluid. Lower seal faces are made of hard materials such as tungsten carbide or silicon carbide for abrasive service and feature different finishes (polished vs. matte) to prevent sticking. The lower stationary seal is also secured via an anti-rotation pin to keep it in place. A lip seal is used in front of the mechanical seal as an additional sealing measure.
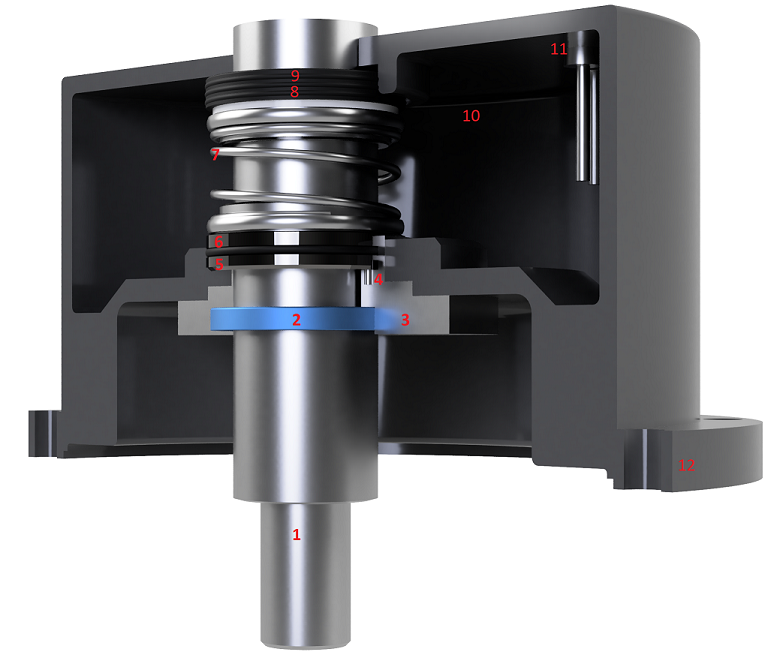
- Motor Shaft
- Lip Seal
- Seal Gland
- Anti-Rotation Pin
- Lower Stationary Face (Tungsten Carbide or Silicon Carbide)
- Lower Rotating Face (Tungsten Carbide or Silicon Carbide)
- Seal Spring
- Upper Rotating Face (Carbon)
- Upper Stationary Face (Ceramic)
- Seal Oil Chamber
- Moisture Detection Probes
- Motor Mounting Flange to Pump

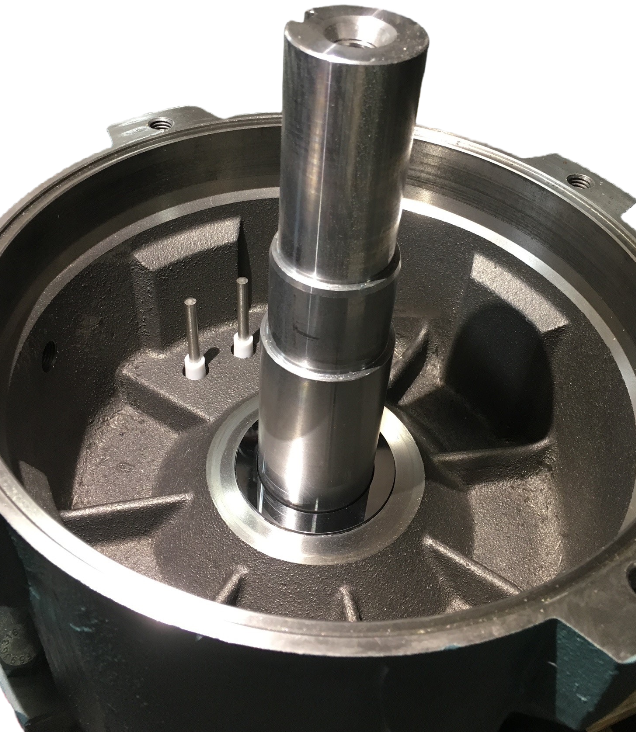
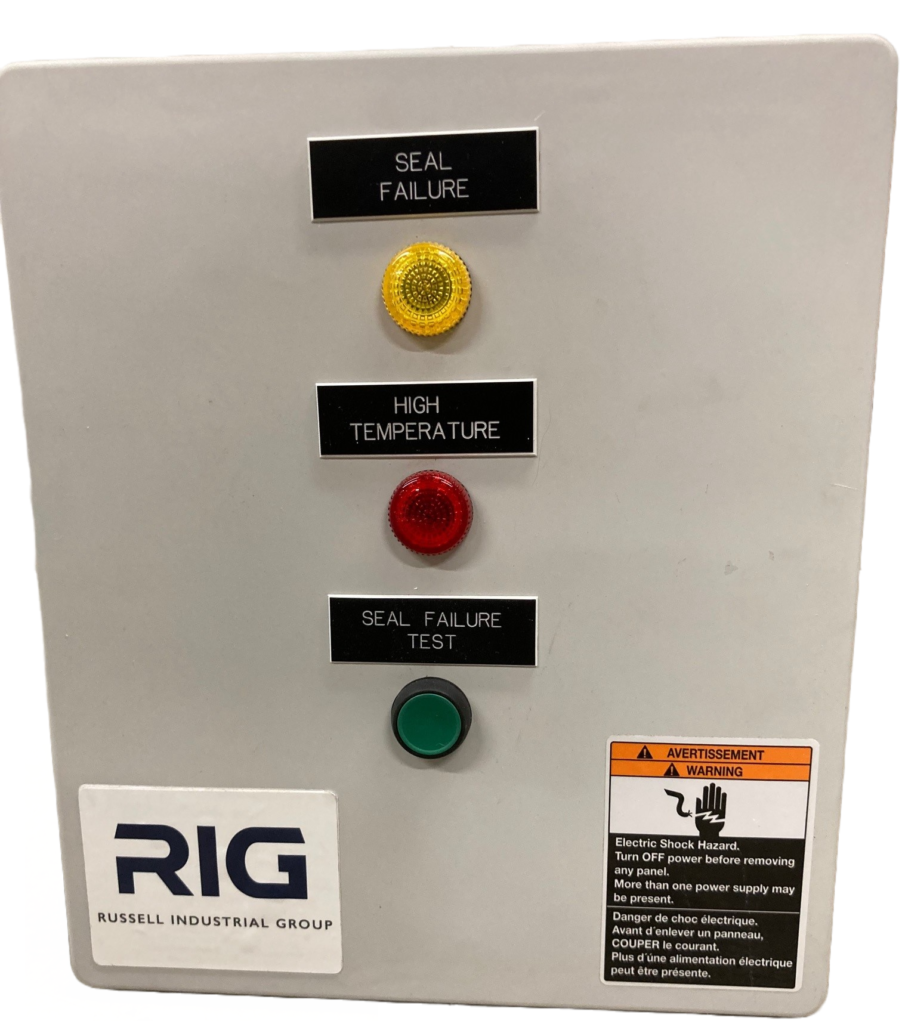
Moisture probes are located in the oil chamber and when used with a relay box will notify the user of seal failure.
Advantages
- Doesn’t see process fluid
- “Run dry” capable
- Cost effective
Limitations
- Submergence max 65′
- No UL rating (only FM)
- Not customizable
The next article will focus on the other seal option, the Tandem Slurry Seal.