Products
R-Series
The engineered severe duty submersible slurry pump customized for the world’s most demanding abrasive and corrosive applications.
Rugged. Reliable. Relentless.
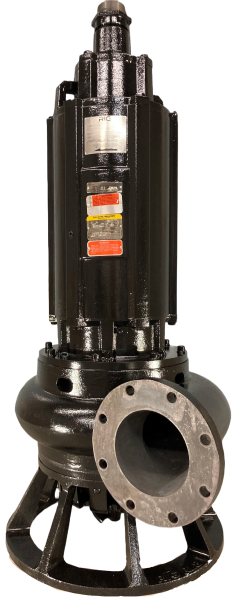
Overview
- 11 different liquid end sizes (2″-8″ discharge with low, medium, high head options)
- Trimmed impellers and several motor speeds to hit specific duty points
- Various materials of construction for castings, machined parts, and hardware
- Liquid temperatures up to 194F / 90C
- Optional agitator and discharge elbows
- Several mechanical seal and motor configurations
- Castings and machined parts made in the USA
- Assembled pump coated in ErgonArmor Novocoat SP2000W for superior protection
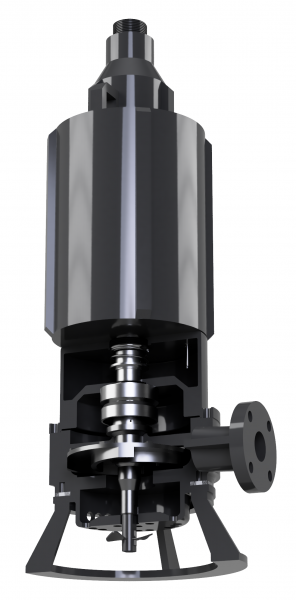
Liquid End Features and Options
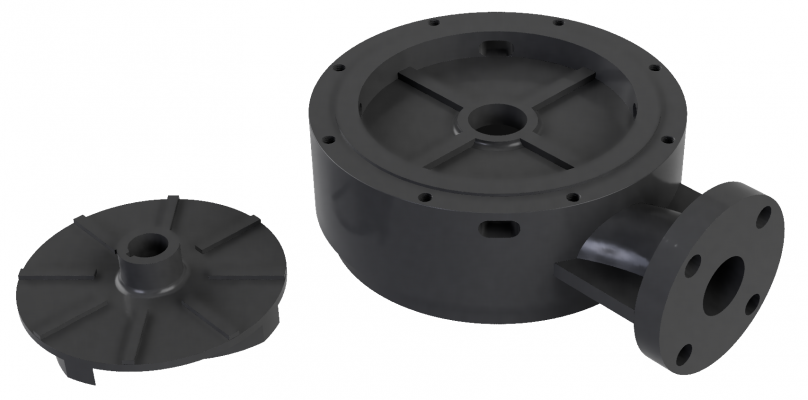
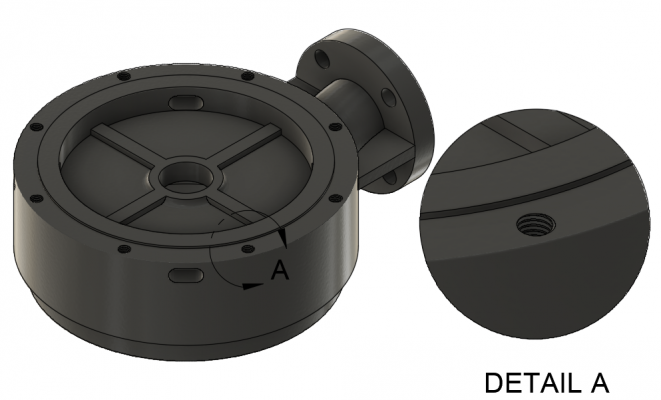
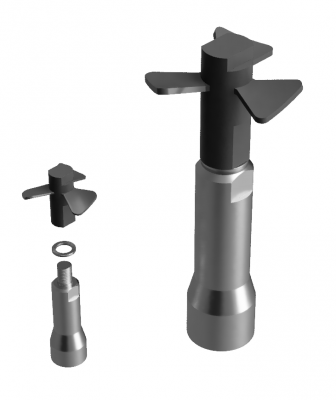
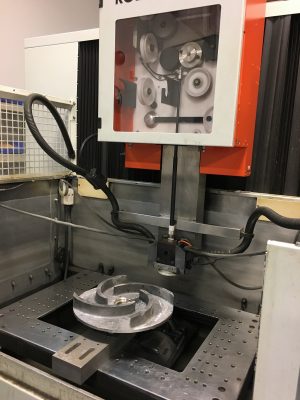

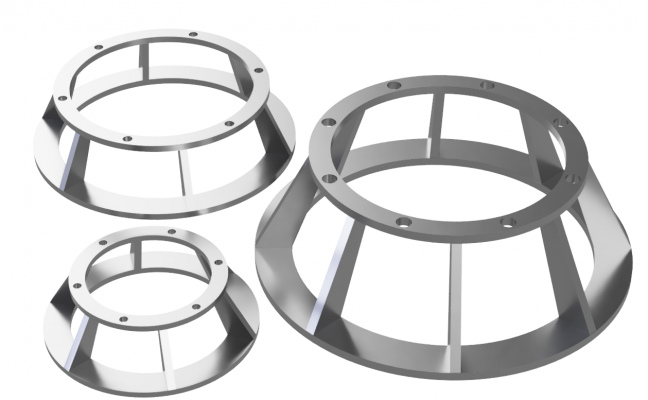
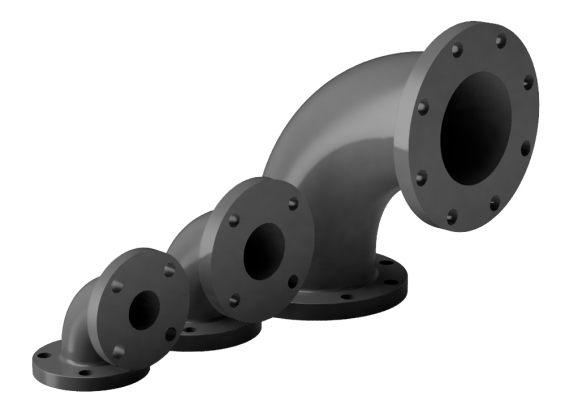
Material Options
These material options can apply to pump castings (casing, impeller, suction/motor covers, agitator, elbows), machined parts, hardware, and motor shafts. Castings and machined parts are proudly made in the USA.
- High Chrome Iron (ASTM A532 Class III Type A) Extreme Abrasion Resistant
- 316 Stainless Steel (ASTM A743 CF8M) Corrosion Resistant
- Duplex Stainless 2205 (ASTM A890 Gr. 4A CD3MN) Corrosion/Abrasion Resistant
- Duplex Stainless CD4 (ASTM A890 Gr. 1B CD4MCuN) Corrosion/Abrasion Resistant
- Super Duplex 2507 (ASTM A890 Gr. 5A CE3MN) Enhanced Corrosion/Abrasion Resistant
- Alloy 20 (ASTM A743 Gr. CN7M) Enhanced Sulfuric Acid Resistant
- Alloy C276 (ASTM A494 Gr. CW12MW) Extreme Corrosion Resistant
Hydraulic Coverage
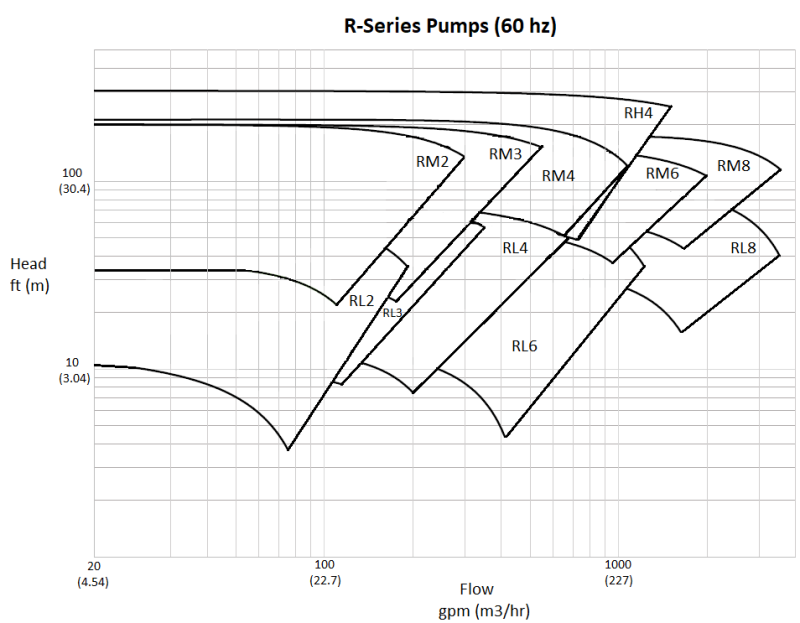
Motor Features and Options
- 2 motor suppliers (EIM and ABB Baldor) with heavy duty construction
- FM Approved and UL Listed for Cl. I Div. I Groups C & D Hazardous Locations (explosion proof configurations)
- Built in thermal overload thermostats. Wired for moisture detection (seal failure alarm) with 2 probes in oil chamber
- Class F insulation (104F / 40C fluid temperature) standard. H insulation options up to 194F / 90C
- Custom power and control cable lengths available
- Continuous in Air (full dry run) configurations available. 316 stainless construction available.
- Available in custom voltage. VFD capable.
- 2 mechanical seal configurations
John Crane Type 5840 Slurry Seal
The 5840 seal is an outboard cartridge seal for ABB Baldor submersible motors only. It is used in conjunction with a single John Crane Type 21 internal seal (carbon/ceramic faces) in the motor oil chamber. This provides for a tandem seal arrangement with two independent seal systems. This is the most robust seal design offered with higher pressure and radial runout allowances with minimal exposed parts.
- 2205 duplex stainless construction standard (2507 super duplex and C276 optional)
- Silicon carbide seal faces
- Encapsulated spring
- Primary ring secured by set screws
- Secondary ring secured by anti-rotation pin
- O-ring fits
- Can be used on motors for UL Listed Cl. I Div. I Groups C & D locations
- Seal can often be repaired vs. replaced for lower maintenance cost
- See more at John Crane
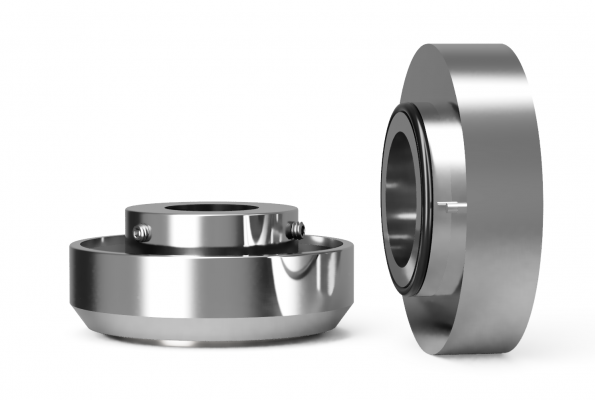
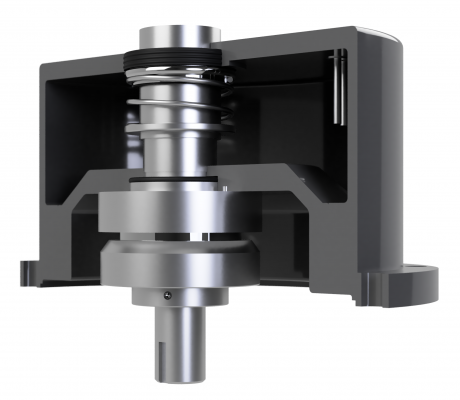
Internal Double Slurry Seal
Both EIM and ABB Baldor motors can use this seal configuration. It is a back-to-back double seal configuration where two sets of faces share a single spring. The entire assembly operates in the motor oil chamber and does not see the process fluid. This seal is also protected by a lip seal as the first barrier of protection. This seal is great for less severe applications and is more cost effective than the 5840.
- EIM motors use Eagle Burgmann ED560 with silicon carbide lower (process) faces and carbon ceramic upper faces
- EIM motors carry FM Approval for Cl. I Div. I Groups C & D hazardous locations
- ABB Baldor motors use a John Crane Type 21 double seal with tungsten carbide lower faces and carbon ceramic upper faces
- Stainless steel (316 and 304 construction) with fluoroelastomer bellows
- O-ring fits for stationary faces
- Lower stationary face is further secured via anti-rotation pin
- See more at Eagle Burgmann and John Crane
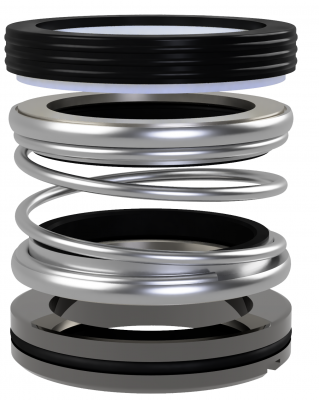
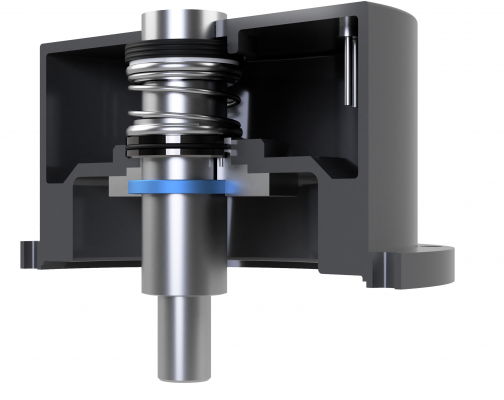

Accessories
- Pump controls and starter panels with moisture detection and thermal overload alarms
- Rubber slurry discharge hoses
- Stainless steel spray rings
- Stainless steel pump lifting bails
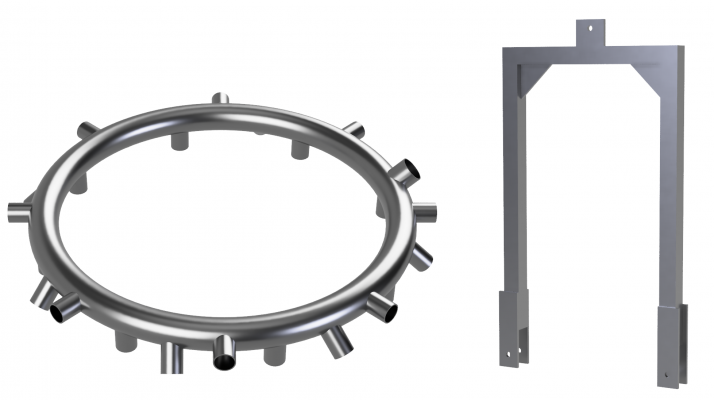
Get in touch for any quoting, distributor, or technical questions.